PRODUCTS AND SERVICES provided by SPARTACUS
The developments made in the SPARTACUS projects led not only to a deeper understanding
about sensor based battery monitoring data and SoX,
but also to SERVICES and PRODUCTS provided by the SPARTACUS team for further application.
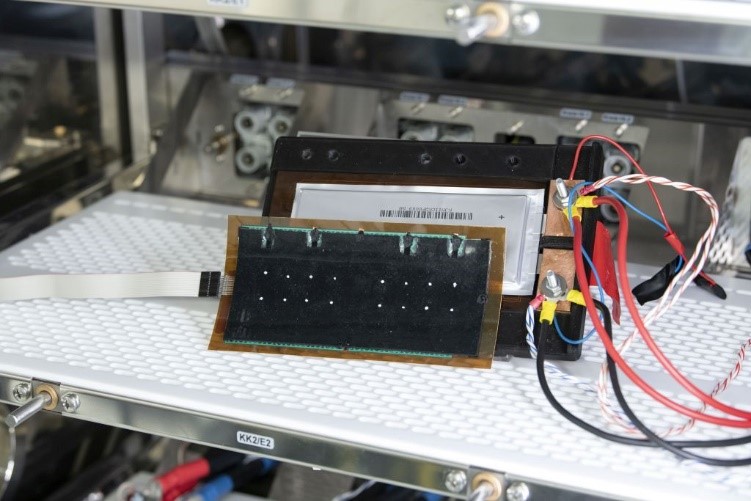
Dielectric elastomer sensors adapted for monitoring compression load of clamped battery cells. Copyright Fraunhofer ISC
Johannes Ziegler, Detlev Uhl, Holger Böse
Proceedings Volume 12482, Electroactive Polymer Actuators and Devices (EAPAD) XXV; 124820J (2023) https://doi.org/10.1117/12.2658246]
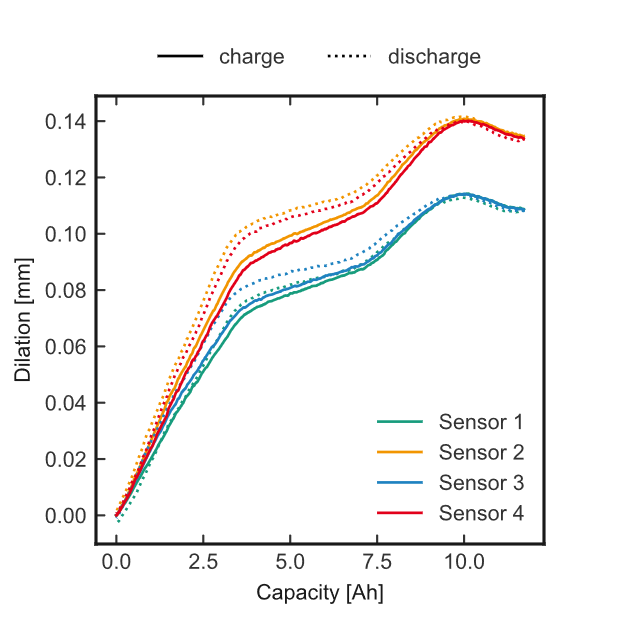
Dilation over Capacity and differential Dilation dx/dV over Voltage for 4 sensors. The data shows that the thickness changes during a C/10 cycle can be measured. Significant thickness changes were measured at the expected phase transitions of the active material. Copyright Simon Feiler et. al., Fraunhofer ISC, Battery 2030 Annual Conference,May 9-10th 2023, Uppsala (Sweden)
Battery cell separating layer with integrated dilation sensors
As part of the SPARTACUS project, dielectric elastomer sensors from Fraunhofer ISC were adapted to the specific requirements for detecting volume changes in battery cells. The elastomer sensors perform several essential functions in one material:
- Detection of cell expansion: As capacitive deformation sensors, they measure very accurately the dynamic volume changes of the cells during charging and discharging. In addition, they also detect the irreversible and permanent volume change due to cell aging.
- Mechanical decoupling: As elastomers with readily adjustable compression modulus, they separate the cells in a battery module from one another and, as a continous damping layer, ensure a more uniform pressure distribution to the individual cells. Pressure peaks that accelerate cell aging can thus be avoided. They also provide thermal shielding, which can be further optimized depending on the application.
Interested in the SPARTACUS sensors? Please contact us!
Specifications deformation sensor
Type of data | Value/range | Note |
Measurement of cell volume changes in z-direction | 10 … 300 µm | adaptable range, depending on expected cell expansion (dynamic/static) |
Sensor sensitivity: dilation | 0,16 pF/µm | |
Absolute sensor sensitivity: dilation | 3 µm | depending on preload |
Sensor sensitivity: compression load | 0.78 pF/kPa | |
Absolute sensor sensitivity: compression load | 2 kPa | depending on preload |
Size of sensor element | 2 cm x 2 cm | size of one sensor element |
Mechanical pre-load | 25 kPa | beneficial for enhanced cell lifetime |
Compression modulus | 300 kPa | optimized stiffness for homogeneous pressure dispersion (adaptable) |
Size of sensor array | Depending on battery cell | adaptable to battery cell dimensions |
Sensor thickness | ~ 2 mm | low installation space |
Weight | low weight | polymer density ~ 1 g/cm³ |
Sensor array | locally resoluted | multiple sensors possible on battery cell surface |
Lateral resolution | 2 cm x 2 cm | minimum: 0.5 cm x 0.5 cm |
Sensor electronics | microcontroller-based | low energy consumption |
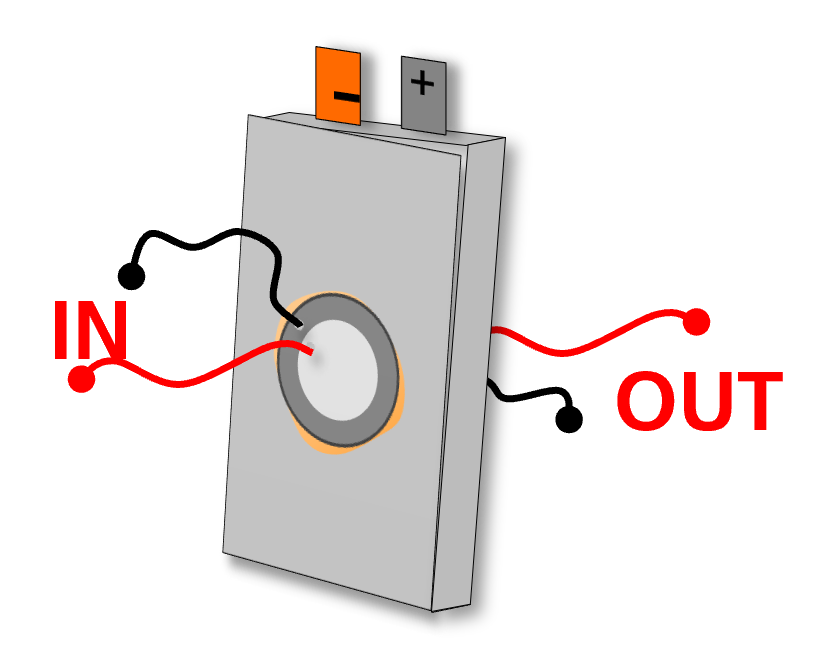
Picture 1 shows the basic construction using the example of a pair of transducers. Preliminary tests have shown that an excitation with raised cosine pulse with five oscillations (RC5) provides short and easy to interpret measurement signals. Copyright Fraunhofer ISC
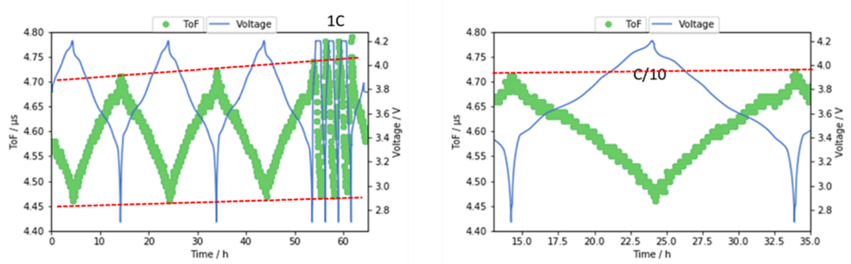
Measurements with PZT disc transducers (@ 2 MHz) on sensor sheets directly on a KOKAM battery cell showed the dependency on SoC and charging rate. During charging the electrodes become denser and stiffer which yields to a shorter transmission time of the US wave. The drift of ToF – amplitudes is caused by battery heating (measured separately and dependent on charging rate). Copyright Fraunhofer ISC
Detection of mechanical cell properties by ultrasound
Ultrasound is used for structural monitoring and thickness measurement of components. For continuous monitoring of the state of charge and the chemical (ageing) processes inside a battery, the interaction of the ultrasonic waves with differently dense and hard individual layers (lithium de-/intercalation in electrodes) can be used.
The principle requirements for the ultrasonic transducer on the measuring foils within a battery pack are:
- Small size (max. 20 mm in diameter, small thickness (max. 1-2 mm))
- Simple and inexpensive components and construction
- Compatible with processes for mounting additional sensors
- Wide frequency range (100 kHz – 10 MHz)
Specifications ultra sonic sensors (piezo)
Type of data | Value/range | Note |
Measurement of cell thickness changes in z-direction | 30 … 2000 µm | |
Sensor sensitivity to battery thickness | 10 µm | |
Sensor sensitivity to Young´s modulus | 100 MPa | |
Size of sensor element | diameter 10 – 50 mm | |
Sensor thickness | 1 – 2 mm | depending on resonance frequency |
Sensor array | Locally resoluted | Multiple sensors possible on battery cell surface |
Lateral resolution | 2 cm x 2 cm | Minimum: 0.5 cm x 0.5 cm |
Sensor electronics | Microcontroller-based | low energy consumption |
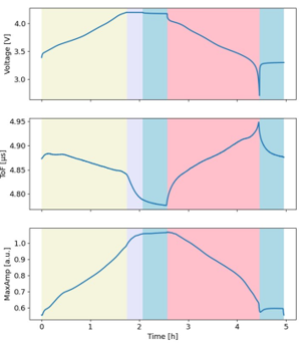
Picture 1 shows voltage, ToF, and maximum amplitude during C/2 charge and discharge. C/2 constant charge to 4.2V and constant voltage charge to 0.05A; CV charge; Rest 30 min; C/2 discharge to 2.7 V; Rest 30 min. Copyright VUB
Advanced battery modeling
In the context of ultrasound, the Time of Flight (ToF) and maximum amplitude undergo significant changes during battery charge and discharge processes, potentially coming from:
- Cell thickness change and
- Stiffness change of electrodes.
The similar effects can be witnessed when speaking of acoustic measurements, measurements of the cell expansions during the operation. These changes correlate with the State of Charge (SoC) of the battery thus allowing for the extra layer of the supervision of the battery states beyound the conventional current and voltage measurement.
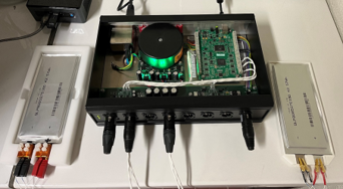
Picture 1 shows an ORP-EIS sensor with multiplexer connected to 2 battery cells. Copyright VUB
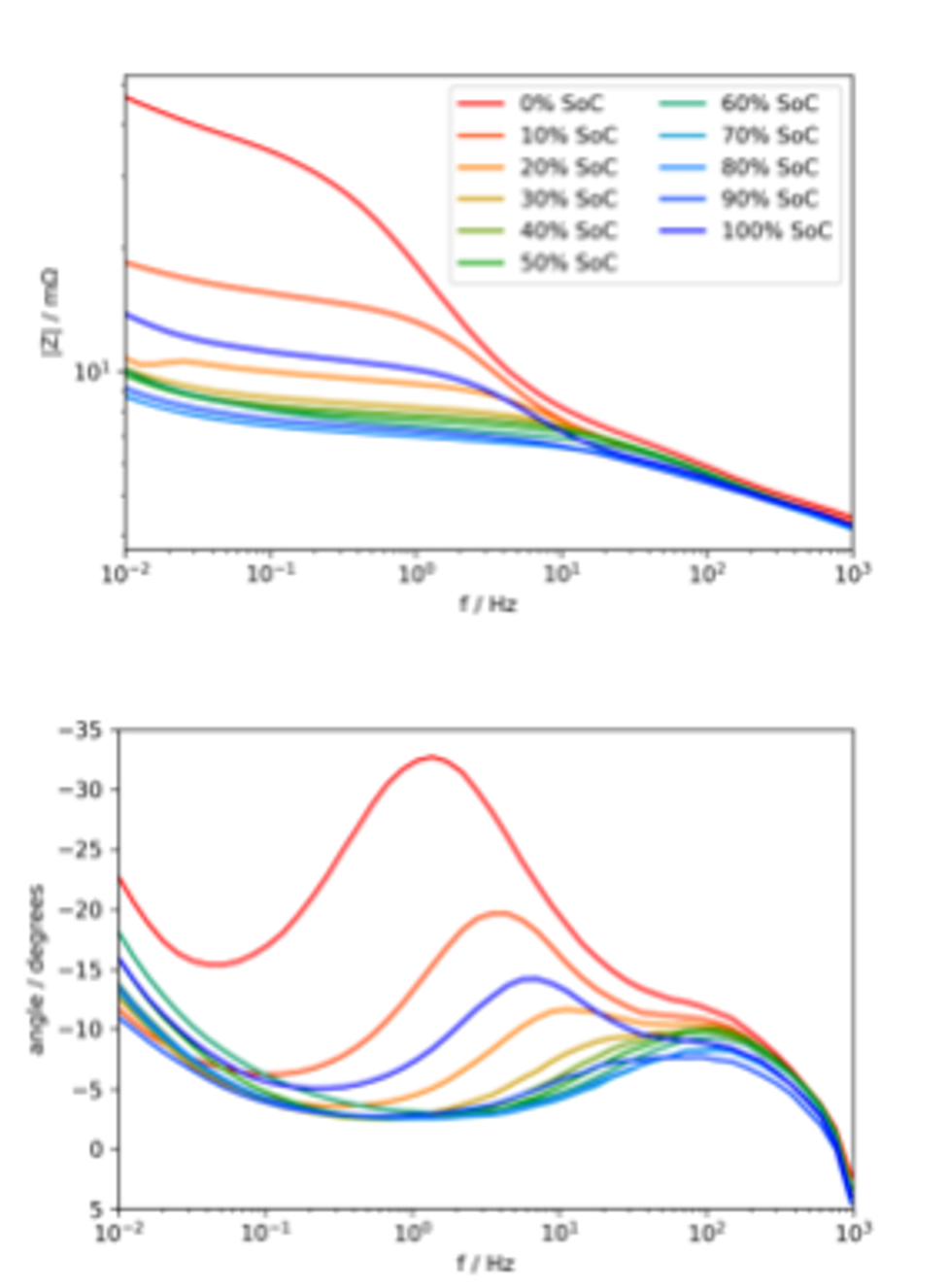
Impedance response of the KOKAM cell as a function of the state of charge. Three time constants can be identified clearly; mass transfer at low frequencies, charge transfer at middle frequencies and SEI layer capacticane at high frequencies. Copyright VUB
ORP-EIS sensor
For the SPARTACUS project, the ORP-EIS technique was implemented in a standalone sensor to measure the impedance of the battery cells. The impedance provides information on the state of charge and the state of health of the cell. ORP-EIS stands for “Odd Random Phase Electrochemical Impedance Spectroscopy”, this is a multisine technique that measures all excited frequencies simultateously, providing a shorter measurement time. The measurement validity can by analysed by looking at the different noise levels of the measurement.
Specifications ultra sonic sensors (piezo)
Type of data | Value/range | Note |
Impedance range | 10 µohm – 10 ohm | |
Excitation current | 200 mA RMS | can be lowered for higher impedances |
Frequency range | 10 mH – 1 kHz | additional frequency ranges available for faster measurements |
Sample rate | 3 ksps | |
Analog input resolution | 18 bit | |
Sensor electronics | Intel NUC-based |

Got any questions?
Don’t hesitate to contact us!
Project Coordinator
Gerhard Domann
Fraunhofer ISC
gerhard.domann@isc.fraunhofer.de
————————————————–
Dissemination Manager
Marie-Luise Righi
Fraunhofer ISC
marie-luise.righi@isc.fraunhofer.de